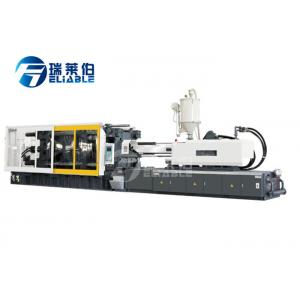
Add to Cart
Hot Popular Automatic Used Plastic Injection Molding Machine
Used Plastic Injection Molding Machine---Machine Introduction
Parts of injection molding machines
1.Clamping Unit
Reliable design with 5 pivot diagonal toggle;Twin-cabinet structure with high rigidity;
Automatically adjusting the position of mould;
2. Injection Unit
According tothe product production needs, free choosing different
diameters of screws;
Control the charge back pressure through a pressure valve
Matching accumulator as to promote the injection performance
3. Control System
Configured with imported hydraulic and electrical components of high
Quality
4. Hydraulic System
Advanced hydraulic system design, through proportional control of pressure, flow achieves
rapid multi-level pressure, speed switching, the system configuration is reasonable, stable and
reliable.
MOLD CLAMPING PART
The inverted double-toggle three-rod five-hinge mold clamping structure with the optimized design features as the balanced movement, large mold moving stroke, fine rigidity. Four-step mold clamping pressure, speed, differential quick clamping device has the multiple ejection modes and functions.
-Horizontal double-toggle five-hinge hold-in design. It utilizes its own structural features to increase the opening stroke and rod pitch etc. Meanwhile it avoids hurting the mold (small machine) because of inclined mold board due to uneven force caused by dead weight of vertical parts.
-Up/ down double-toggle five-hinge hold-in design (medium and big machines)
-High rigidity, high intensity box style integrated mold board analyzed by finite element reduces the accumulated error caused by the multiple processing and assembly. It thus increases the mold clamping accuracy.
-It applies quantitative automatic lubricating system. It regularly or sequently executes quantitative oil supply to various lubricating points. It is effective and economical.
-Low-pressure mold protection function prevents from mold damage.
-Mold clamping structure has mechanical, electrical and hydraulic triple safety devices. It is used to ensure the staff security.
-It is of high automatic mold adjusting precision. In renewing the mold, it can fulfill self-adjustment of mold clamping force through setting the parameters.
-Quick mold clamping system applies oil-pressure differential circuit. It increases mold clamping speed, reduces the forming cycle.
-High intensity rod plated with hard chrome matches with automatically lubricated copper wire. It is of smooth movement and long life.
Ejector pin applies position transducer control. It brings about the accurate forward and backward positioning
·It applies the world's famous brand metering pump and control valve. It accurately controls the force and speed of hydraulic mechanism in an energy-saving way. It ensures the precise and reliable machine operation.
·It applies the durable imported sealing parts.
·The clear and concise oil pipe distribution reduces energy loss caused by oil circuit. It is convenient for repair and maintenance.
·The unique oil-circuit design not only reduces the noise, but also increases radiating surface to the greatest extent. It reduces oil temperature, usage amount of cooled water. It increases the service life of oil-circuit hydraulic sealing parts etc.
·New generation intellectual central controller with high precision and high stability Automatic trouble diagnose and alarm system.
·It executes real-time temperature display function.
·Charging barrel temperature applies PID control mode.
·The multiple modes of core pulling and ejector pin functions.
·Production data storage, printing output function.
·Display function of injection speed / pressure chart
·Automatic open/shut the machine or turn
·Mechanical arm interface loop
·It applies large screen LED display screen. It support thultiple nations' language system
·It applies high speed and high precision German NOVO position sensor to ensure the position control accuracy.
Technical Paraments
Unit | DS-320T | |||
A | B | C | ||
Injection unit | ||||
Screw Diameter | mm | 60 | 65 | 70 |
Screw L/D Ratio | L/D | 23 | 21.2 | 19.7 |
Shot Size(Theoretical) | cm3 | 918 | 1078 | 1250 |
Injection Weight | g | 806 | 946 | 1097 |
Injection Pressure | Mpa | 190 | 162 | 140 |
Plasticizing Capacity | g/s | 35 | 40 | 43 |
Screw Speed | rpm | 0-200 | ||
Clamping unit | ||||
Clamp Tonnage | KN | 3200 | ||
Toggle Stroke | mm | 590 | ||
Space Between Tie Bars | mm | 630*610 | ||
Max.Mold Height | mm | 650 | ||
Min.Mold Height | mm | 220 | ||
Ejector Stroke | mm | 160 | ||
Ejector Tonnage | KN | 71 | ||
Ejector Number | PC | 9 | ||
Others | ||||
Max.Pump Pressure | Mpa | 16 | ||
Pump Motor Power | KW | 30 | ||
Heater Power | KW | 18 | ||
Machine Dimension(L*W*H) | m | 6.6*1.8*2.3 | ||
Machine Weight(About) | T | 10 |